1 - Généralités :
Pour le”simmer”, une CNC permet la découpe et la gravure des panels, et la réalisation de nombreuses petites pièces relevant facilement du fraisage, comme par exemple les korrys ; plexi (PMMA), delrin (POM), PVC, alu (là, il faut déjà une machine d’un certain niveau), le champ des matériaux facilement usinables est large ; la précision d’usinage dépasse largement le 1/10 mm ; c’est l’outil qui permet réellement d’atteindre un bon niveau de réalisme.
3 logiciels sont nécessaires, CAO ou DAO pour le dessin des pièces, FAO (en l’occurrence CAMBAM) pour définir les consignes d’usinage, et un logiciel de pilotage de la CNC, ici MACH3.
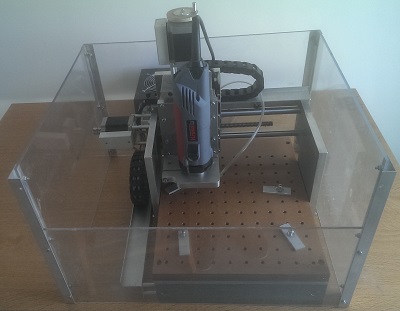
J’ai acheté ma première CNC, vue au Mondial du modélisme en 2012, une des premières machines accessibles à l’amateur, origine Suisse ; la mise en route a été longue et laborieuse, pièces abîmées, structure insuffisante, géométrie bancale, et j’en passe, je ne m’attendais pas à ça de la part d’une fabrication suisse ; support déplorable, une mauvaise expérience ; j’ai remplacé quelques pièces, rajouté d’autres pièces, rajouté des roulements, modifié l’électronique de commande, et ai obtenu finalement une bonne petite machine, précise et robuste, avec laquelle j’ai même pu à m’attaquer avec succès au fraisage de l’alu.
Attention, la courbe d’apprentissage pour une telle machine n’est pas négligeable : outre l’apprentissage d’une CAO et d’une FAO, il faut également acquérir quelques notions d’usinage, car pour obtenir des résultats corrects, il faut respecter des règles précises et qui ne s’inventent pas. Mais la littérature est abondante, comme également les forums et sites spécialisés.
Cette première machine m’a permis de réaliser la première version du simu, avec cependant quelques restrictions : une surface de travail modeste, imposant de fréquentes opérations de reprise, et une capacité d’usinage très limite pour le fraisage de l’alu. L’idée de réaliser une machine plus conséquente m’est venue, une fabrication à base de profilés alu me semblant accessible avec mon outillage de bricoleur moyen ; mais, sur les forums, de nombreux esprits chagrins laissaient entendre qu’une telle conception ne pouvait mener qu’à l’échec : complètement stimulé par ces déclarations un peu rudes, j’ai ressorti mes ouvrages de résistance des matériaux, ma calculette, et ai commencé à modéliser la chose avec Turbocad ; après 3 bons mois, j’étais prêt !
Au cahier des charges :
– surface de travail de 800×550 (mm, en mécanique c’est l’unité par défaut),
– construction tout alu, outillage standard,
– précision d’au moins 1/20,
– broche 5000/20000 trs/mn,
– usinage alu dans de bonnes conditions, usinage acier à faibles passes.
2 - Préparation :
La machine est constituée de profilés alu et de plaques d’alu (2017, ex AU4G, bonne résistance mécanique, facilement usinable, contrairement par exemple à l’alu de GSB !) ; la première tache a été la découpe et le perçage de toutes ces plaques, épaisseur 10, 15 et 20, précision des découpes et perçages de l’ordre du 1/10.
Plusieurs sites sur internet propose des métaux courants aux particuliers, dont de l’alu en diverses nuances et dimensions pratiques (300×500), livraison rapide.
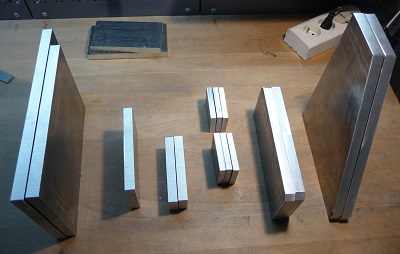
La phase de découpe est physique ! faute de scie à ruban, la tôle d’alu se coupe bien à la scie sauteuse (pendulaire), lame spéciale alu ; il faut solidement fixer la tôle, lubrifier régulièrement au pétrole (avec un pinceau), et scier en poussant ferment mais pas trop, et en laissant une marge d’environ 1 mm ; ça ne va pas très vite (de l’ordre de 1 cm à la mn), et ça use … je devrai changer en cours de route la roulette guide lame, pratiquement fendue en deux !
Une fois cette phase terminée, ouf, il faut mettre les champs d’équerre et aux bonnes cotes, là aussi ça donne chaud :
– j’ai d’abord dégrossi et mis d’équerre à la ponceuse à bande, bien fixée sur le dos, gros grains : ça “déménage” sérieusement, ne pas oublier de s’aider d’une cale pour assurer la bonne orthogonalité des champs ; vérifications fréquentes au pied à coulisse, on s’arrête à environ 2/10 de la cote.
– la finition requiert une ponceuse à disque fixe ; j’ai acquis pour la circonstance une Proxxon à disque de 250, c’est devenu un outil absolument indispensable ! table réglée bien perpendiculaire au disque, abrasif grain moyen, pied à coulisse entre les dents, on atteint facilement la cote au 1/10.
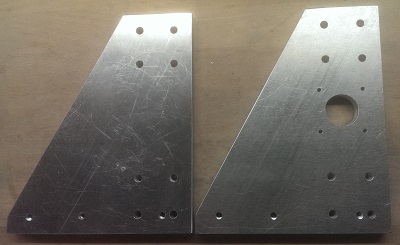
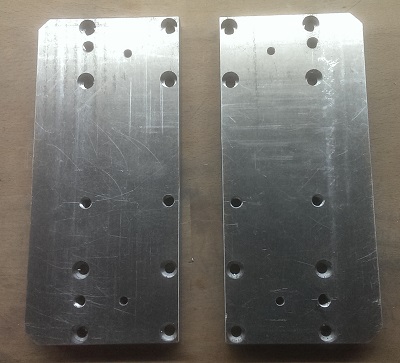
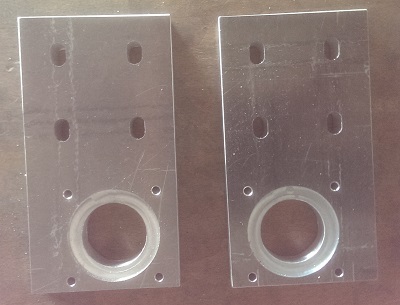
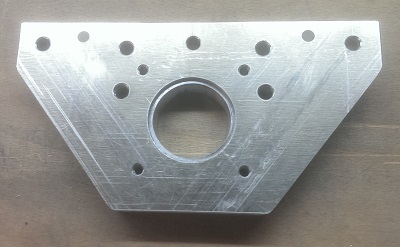
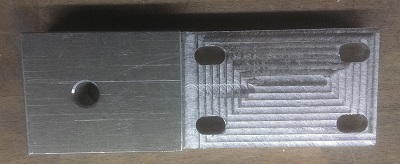
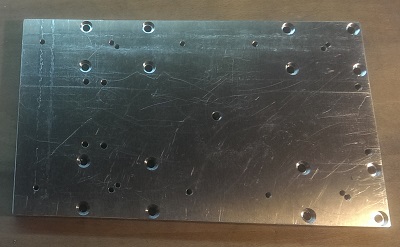
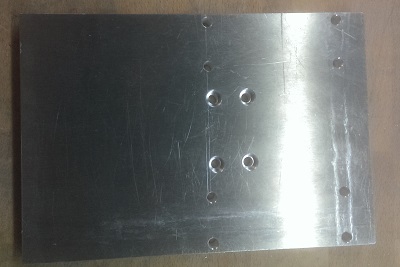
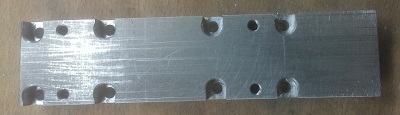
Dernière opération, les perçages et lamages :
– d’abord traçage et pointage précis (il faut d’abord un peu s’entraîner, sinon il faudra par la suite agrandir des trous !) ; cette opération est vraiment cruciale, pas d’à peu près !
– puis perçage : une vraie perceuse à colonne est indispensable, et des forêts spéciaux pour l’alu fortement souhaitables ; idem pour l’encastrement des têtes de vis, fraise à lamer indispensable.
Quelques pièces requièrent des usinages complémentaires : trous pour le centrage des moteurs, lamage pour la fixation des écrous de vis à bille ; j’ai utilisé ma première cnc, mais scie et lime auraient pu suffire.
3 - La base :
Pour la suite, les profilés alu entrent en scène : à ce stade, un fournisseur allemand s’est rapidement imposé : large choix et découpes très précises.
Ce sont les caractéristiques de ces profilés qui m’ont décidé à me lancer dans cette construction : fixations simples par vissage, et capacités mécaniques très intéressantes : j’ai retenu des profilés de section 80×80 et 160×80 ; leur moment d’inertie sont de 135 cm4 et 135 cm4 pour le premier, et 903 cm4 et 266 cm4 pour le second ! les calculs de rdm en statique montrent que les déformations de structure en flexion sont bien inférieures à la précision que je vise, et des esquisses de calcul en régime dynamique me laissent bien augurer.
Le poids de ces profilés est également significatif, c’est un facteur essentiel pour l’absorption des vibrations ; ces caractéristiques sont encore éloignées de celles de l’acier, mais les dimensions que j’ai retenues permettent d’envisager une structure rationnelle et suffisamment lourde et rigide, facteur important pour le fraisage courant de l’alu.
La base est donc constituée de 2 longerons latéraux de 80×160, réunis par 3 poutres transverses de 80×80, assemblage par grosses équerres. 3 longerons centraux de 40×80 complètent l’ensemble pour offrir une bonne assise à la table.
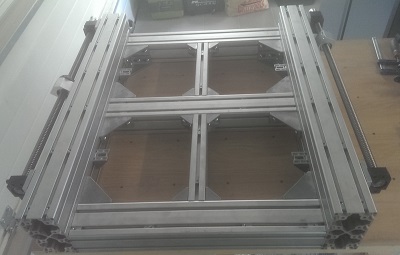
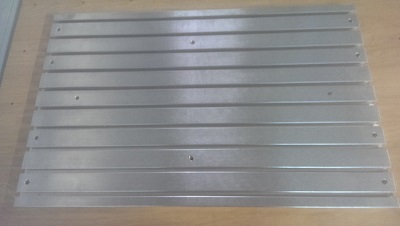
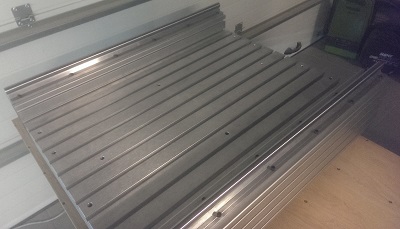
Sachant qu’un jour ou l’autre j’en viendrais à une table alu rainurée, j’ai choisi d’en acheter une tout de suite (origine allemande) de bonne qualité ; elle est livrée avec un certificat (relevés de planéité), on est dans des écarts de 2 à 3/100 au maximum.
A ce stade, le rôle de cette table est central : elle constitue en effet ma référence géométrique, tant en planéité qu’en orthogonalité. Car il faut dès maintenant s’assurer de la parfaite géométrie de l’ensemble ; cette étape est fastidieuse mais essentielle, il faut user de l’équerre, du comparateur, de clinquants de diverses épaisseurs, serrer, desserrer, resserrer jusqu’à être satisfait : toute concession à ce stade se traduira par des erreurs systématiques lors de l’usinage.
Une fois ces réglages satisfaisants, vient le montage des rails, il s’agit ici de rails cylindriques supportés de type TBS20 (pas courants, mais présentent des perçages d’entre-axe 40, ce qui coïncide avec l’écartement des rainures des profilés). Pourquoi des rails cylindriques et non des rails prismatiques (aux performances supérieures) ? pour une basse raison financière ; je le regretterai parfois par la suite, lorsque la machine est fortement sollicitée (fraisage acier), mais ce choix reste cohérent par rapport au reste de la constitution de la CNC.
Nb : des rails cylindriques de 20 sont précis et rigides ; en revanche, ils exigent des patins fendus, qui sous l’effet des contraintes, ont tendance à très légèrement s’écarter, on y perd des 1/100èmes.
Et re-réglages, rail maître parallèle au grand coté référence de la table, et parallélisme du second rail par rapport au premier.
4 - Le portique, le chariot transversal et le chariot des Z :
Le portique se déplace sur la base selon l’axe des X ; il supporte l’axe des Y, sur lequel se déplace le chariot transversal qui supporte l’axe des Z.
Il est constitué de 2 flans en alu de 15 réunis par 2 poutres de 80×80 ; l’axe des Y est là aussi constitué de 2 rails cylindriques supportés de 20, fixés sur chacune des poutres. 2 platines à la base des flans accueillent les 2 paires de patins de l’axe des X.
Une nouvelle séance de réglages s’impose.
Le chariot transversal est constitué d’une plaque d’alu de 15, dotée à son dos de 4 patins qui viennent glisser sur les rails des X : en face avant, ce sont 2 rails prismatiques de 20 qui constituent l’axe des Z ; entre les deux est logée la vis à bille d’entrainement du chariot des Z : vis de 20 au pas de 5, un pallier à 2 roulements obliques en haut (BF15), et pallier à 1 roulement droit en bas (BK15) ; il faut veiller à l’absence de jeux au niveau des roulements obliques, j’ai acheté les paliers en Chine mais ai du remplacer tous les roulements obliques.
Avant de monter le chariot transversal, il faut équiper le portique de la vis à bille d’entrainement du chariot ; même choix que pour l’axe des Z, vis de 20, pas de 5.
Vient enfin le chariot des Z, qui glisse sur les rails prismatiques et porte la broche : il s’agit à nouveau d’une plaque d’alu de 15 au dos de laquelle sont fixés 4 patins prismatiques ainsi que l’écrou de la vis à bille ; pour des raisons simplement géométriques, deux plaques intermédiaires en alu de 20 sont placées entre les patins et la plaque, contribuant ainsi à la rigidifier.
On peut désormais installer cet ensemble chariot transversal et chariot des Z sur le portique, et y fixer l’écrou de vis-à-bille du portique.
Et à nouveau des réglages, et en particulier celui de la bonne orthogonalité du mouvement du chariot des Z par rapport à la table de la base (à ne pas confondre avec celui de l’orthogonalité de l’axe de la broche par rapport à la table).
Les “gros” travaux de mécaniques se terminent avec :
– la fixation des 2 vis à bille de l’axe des Y, vis de 20, pas de 5, de part et d’autre de la base, et la fixation des 2 écrous des vis aux platines basses du portique.
– la mise en place des supports moteurs, 2 en bout de base, et 1 sur le champ haut du chariot transverse ; le moteur des Y est directement fixé sur l’une des flans du portique.
Toute cette construction s’avère plutôt simple si tous les perçages préliminaires ont été conduits avec précision. En revanche, les phases de réglages sont cruciales, un peu délicates et même fastidieuses … mais rien d’inaccessible, même pour un parfait novice (que je suis !).
Les moteurs : très classiquement, 4 moteur pas-à-pas hybrides au format Nema 23 ; sauf à acheter auprès de fournisseurs industriels (chers, chers), il est difficile d’accéder aux caractéristiques complètes de ce type de moteur, le choix est donc difficile, surtout quand on en est à son premier ! et donc mon choix ne sera pas “optimal”, j’ai depuis rectifié.
Il s’agit d’obtenir du couple à une certaine vitesse, ce couple chutant très rapidement avec la vitesse ; pour faire simple :
– pour la vitesse il faut choisir des moteurs à faible inductance et faible résistance, et des drivers acceptant une tension la plus élevée possible,
– pour le couple, il faut bien sur calculer le besoin (prendre en compte les efforts de coupe et les forces d’inertie), et se fier ensuite au couple de maintien du moteur, et de façon corrélée, l’intensité maximale acceptée.
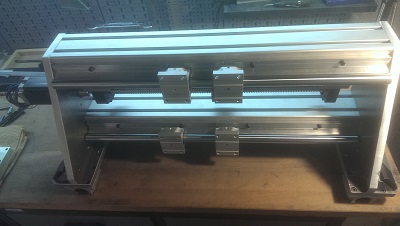
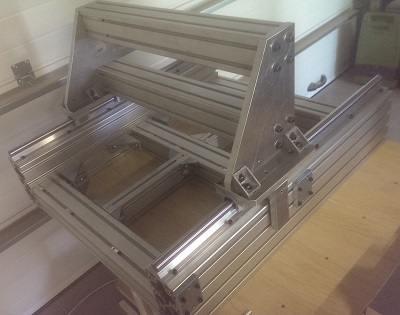
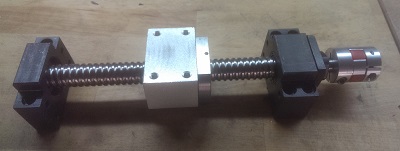
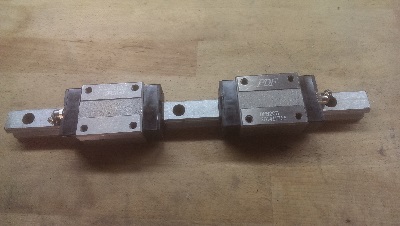
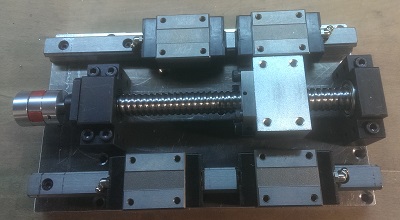
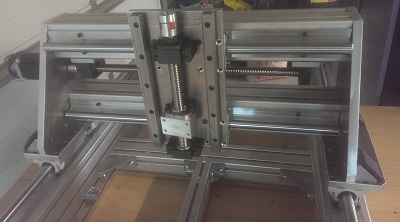
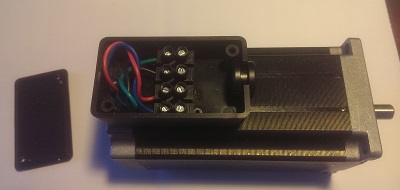
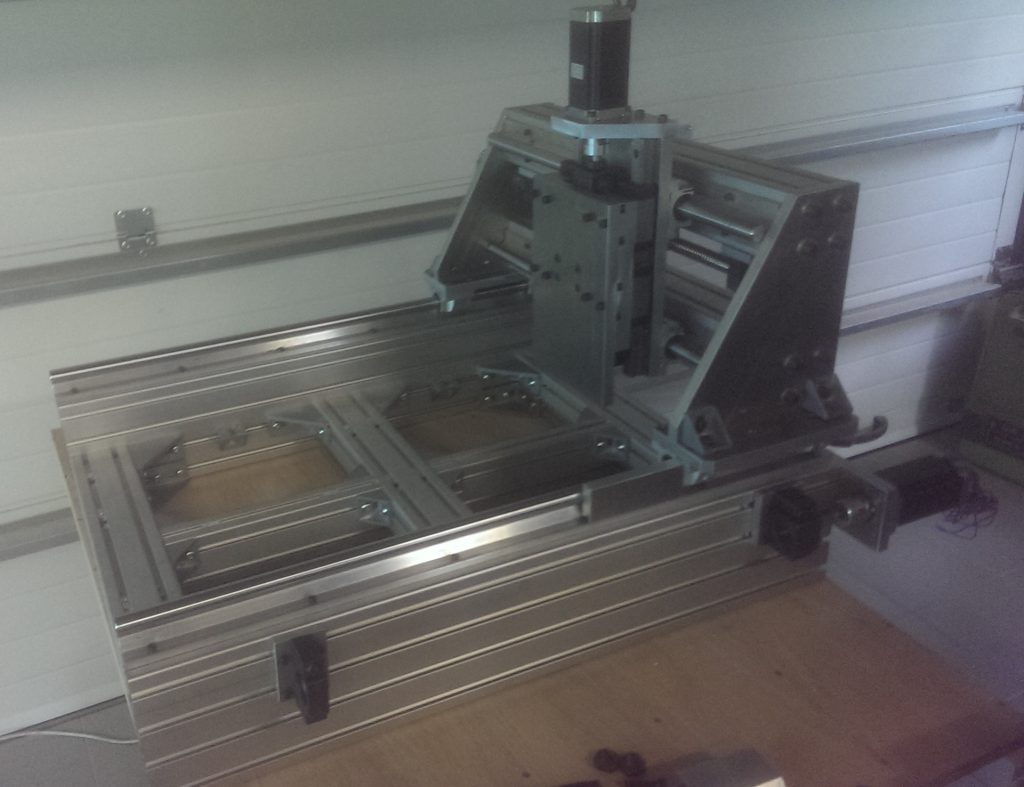
Voici les caractéristiques de mes moteurs :
– Intensité max : 3A.
– Résistance par phase : 0.8 Ohm.
– Inductance par phase : 1.8 mH.
– Couple de maintien : 220 N.cm (avec une vis à bille de 20 au pas de 5, ça fait pas loin de 3000 N, à mettre au regard des efforts de coupe, de quelques dizaines de daN).
– Alimentation des drivers sous 50V DC.
Pour le câblage des moteurs pàp, j’ai collé au double-face sur leur flan un petit boitier muni d’un passe-fil, dans lequel vient se loger une barrette de 4 dominos).
5 - L'électronique :
La CNC est pilotée par le presque incontournable Mach3, sur un PC dédié sous XP ; interfacage par port parallèle.
L’électronique de commande comporte une BoB basique (break-out board) qui fait l’interface entre le PC et les drivers ; les 4 drivers sont des classiques M542 alimentés sous 48V par une alimentation à découpage 12.5A.
Les drivers sont programmés à 4 micro-steps pour une bonne fluidité des déplacements.
Le tout est installé dans un boitier bien ventilé (ventilateur 220V placé directement devant les radiateurs des drivers) ; il faut être très rigoureux sur le câblage, en particulier sur les blindages et masses, afin d’éviter tout couplage entre courant fort et courant faible, faute de quoi gare aux pertes de pas.
Quelques règles :
– transport des signaux faibles par paires torsadées,
– blindage chaque fois que possible, et en particulier pour tous les câbles entre boitier et machine.
– toutes les masses et blindages reliés en un seul point dans le boitier.
– ne pas faire se côtoyer courant fort et courant faible, l’idéal est que les câbles se croisent à angle droit.
– le blindage des câbles reliant boitier à machine ne sont reliés à la masse que du coté boitier (au corps du connecteur, en l’occurrence db9), le corps du connecteur correspondant sur le boitier étant directement ramené à la masse commune.
– l’alimentation des drivers se fait en étoile.
Je n’ai jamais constaté de perte de pas …
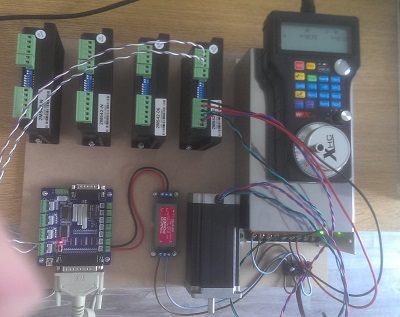
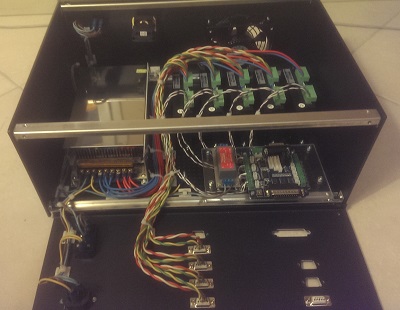
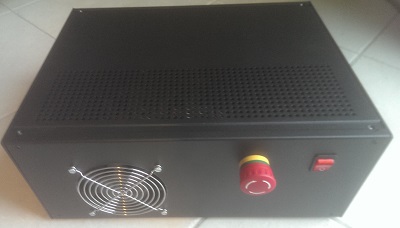
6 - Assemblage final :
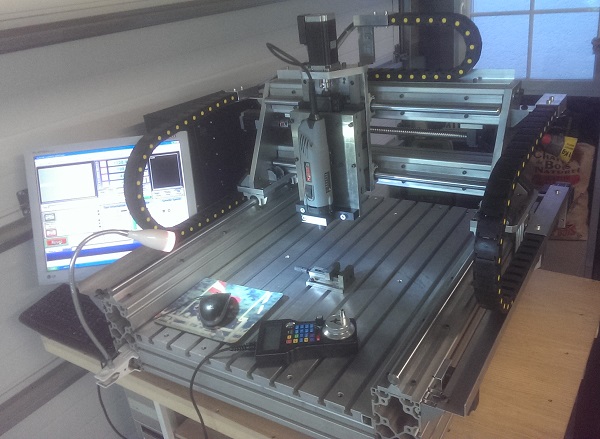
Pour le câblage de la machine, câbles blindés 4 conducteurs pour les moteurs, câbles blindés 2 conducteurs pour les fins de courses (1 seul par axe) ; j’ai opté pour des chemins de câble séparés, de façons à ce que courants forts (les moteurs, l’alimentation de la broche) et les courants faibles (les fins de courses) ne se côtoient qu’au minimum. Les chemins de câble reposent sur des cornières alu, qui les guident et qui protègent les 2 vis à bille latérales.
La broche est une kress 1050 FME-1, puissance 1050W, plage de vitesse 5000/25000 trs/mn ; il est difficile de trouver une broche qui tourne à la fois lentement (pour l’acier, ou l’alu avec une fraise de diamètre supérieur à 6) et rapidement pour le plus tendre ; cette broche est un compromis acceptable ; un peu bruyante mais elle fait le job.
J’ai acheté le support de broche, car je n’étais pas encore équipé pour usiner de l’alu de 20. Un dernier réglage : l’axe de la broche doit être orthogonal à la table.
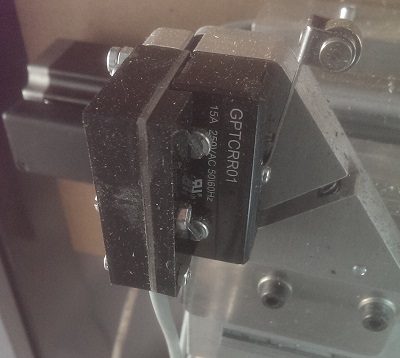
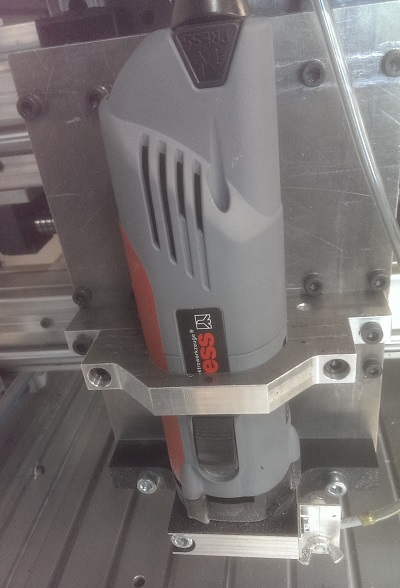
Après un paramétrage sans difficulté de Mach3 (je n’ai pas poussé au maximum vitesse et accélération, juste ce sont j’ai besoin), la machine est directement opérationnelle, mes premiers fraisages dans de l’alu 2017, passes de 1 mm me ravissent ; par la suite, je me cantonnerai à des passes de 7/10 pour ménager un peu la broche.
Mes premiers usinages serviront à terminer la machine, 3 fins de course réglables (qui en fait ne me servent que rarement), et une seconde bride pour la broche, qui en rigidifiant bien l’ensemble chariot des Z-broche, améliorera significativement mes états de surface.
Au bout de 3 ans, je suis vraiment satisfait de cette CNC, utilisation régulière, essentiellement de l’alu, mais aussi de l’acier (j’ai par exemple usiné le chariot orientable de mon petit tour dans de l’acier demi-dur, des petits passes de 2 à 3/10, résultat nickel).
J’ai rajouté un petit dispositif de micro-pulvérisation dont je ne me sers que pour souffler de l’air, cela s’avère vite nécessaire, à la fois pour refroidir mais aussi pour dégager les copeaux qui s’accumulent dans le fond des usinages. Je lubrifie manuellement au pinceau, le pétrole est parfait pour l’alu, huile de coupe pour l’acier.
Au bilan, il est d’une part possible de réaliser une cnc en profilé alu qui se “tient” honorablement dans l’usinage de l’alu, voir un peu l’acier, et d’autre part cette réalisation est accessible au néophyte qui ne dispose que d’un outillage électrique relativement standard (scie sauteuse, ponceuses, perceuse à colonne de GSB).
Bonsoir,
Vos réalisations sont absolument superbes …
Toutes mes félicitations pour votre travail.
Cordialement
Merci Christophe !
Michel
Bonsoir Michel,
Belle réalisation ! et en même temps qui remet un peu les pendules a l’heure quant a ce type de machine.
Je suis sur le point de débuter la construction du châssis de la mienne, j’allais m’orienter sur une version châssis acier tubulaire issus en grande partie d’un plan superbe ceci étant dit trouver sur usinage.com, mais au vue de votre retour d’expérience, j’envisage très sérieusement de faire une version plus ou moins identique a la votre bien plus pratique d’un point de vue conception.
D’autant que mes besoins son visiblement identique au votre (Alu et très occasionnellement acier a faible passe).
du coup plusieurs questions (désolé) pourriez vous m’indiquer le fournisseur des longerons afin d’être sur de choisir une qualité adéquate .
idem pour la table rainurer etc..
Un grand merci d’avance pour votre réponse.
Jimmy
Bonjour Jimmy,
merci pour le commentaire !
Pour une éventuelle réalisation, ça vaux le coup de réfléchir à remplacer les rails cylindriques supportés (en X et Y) par des rails prismatiques de 20, le reste de la machine est tout à fait taillé pour.
Les fournisseurs auxquels je me suis adressé :
– profilés alu : Motedis (bonne géométrie, coupes parfaites),
– tôles al, autres métaux/plastiques : Blockenstock,
– table rainurée : Ironwood, mais je crains que, à date, la société ait disparu ??
– visserie : Bricovis,
– vis-à-bille, paliers, coupleurs, rails et patins : Exmachina-shop, mais je déconseille (mieux vaut un achat direct Chine),
– alim, drivers, moteurs,… : eBay/alibaba.
Michel
Bonsoir Michel,
Merci pour vos information, concernant les rails prismatiques je vais suivre votre conseil .
Merci encore de votre réponse
Jimmy
Bonjour Michel,
J’avance pas mal dans l’étude de ma CNC, du coup je sollicite votre retour d’expérience pour avis.
je dimensionne celle ci dans l’optique d’une surface de travail de 700*400 avec une course Z de 120.
La matiere usinée serait en grande partie de l’alu et un peu d’acier occasionnellement.
D’une manière général je repart sur le principe de la votre concernant le châssis, longeron 160*80 et 80*80 de chez MOTEDIS.
Pour le portique je pense retenir pour les plaques latéral une cote de 300 pour la base et de 400 de haut.
Pour le chariot la plaque de l’axe Z serait d’une largeur de 250 pour une longueur de 375
la plaque supportant la broche serait d’une largeur de 250 pour une longueur de 340
les patins seront espacer au maximum afin de réduire les forces exercées au moment de la coupe.
concernant les différents guidage je pense retenir les guidages prismatique en taille 20 de chez Hiwin en HGH20HA.
Pour les vis a bille je n’ai pas encore d’idée sur la taille et fournisseur, une Idée ?
Merci d’avance pour vos commentaire
Jimmy
Jimmy, quelques dimensions :
– course : 140 (entre bas broche et table), il faut donc y soustraire à minima la longueur sortie de la fraise,
– surface de travail : 540 x 800, pour obtenir la surface utile il faut retirer l’encombrement du Z,
– les flans du portique : 230 à la base, 260 en hauteur, épaisseur 15 (pourrait être 20),
– Le Z : 290 x 170 et 250 x 170, épaisseur 15, plus les intercalaires pour les patins (épaisseur 20), qui font la hauteur du chariot (participent à la rigidité).
Pour les vis, j’ai pris du 20, pas de 5, je ne regrette pas (certains trouveront que du 16 suffirait, mais du 20 va bien mieux tenir dans le temps).
Pour le fournisseur, je ne saurai te conseiller, car celui auquel je me suis adressé ne pas donné satisfaction ! (délais importants, vis tordues, la galère pour obtenir satisfaction) ; sauf si tu es riche, il faut acheter chinois, en établissant avec le fournisseur un contact par mail au préalable.
Michel
Bonsoir Michel,
Merci pour ces précisions, ça m’aide a appréhender la cohérence des différentes cotes.
j’ai augmenté la hauteur et largeur des flans de façon a compenser le porte a faux de l’ensemble chariot et broche, la hauteur me permet d’augmenter l’entre axe des patins pour compenser la course du Z (120) sous fraise et limiter le couple sur les patins.
Concernant l’axe X j’ai vu un montage ou le rail supérieur était monter horizontalement sur la poutre supérieur du portique de faite la plaque 290*170 formais une équerre en partie haute pour accueillir les patins.
que pense vous de ce montage a première vue ça me parais mieux parce que les patins supérieur du coup subisses les efforts de couple en appuis.
quant pensez vous ?
Jimmy
Bonjour Jimmy,
Le rail supérieur du portique au dessus, ou sur le coté, that is the question !
Je me suis posé la question, mais ayant modélisé cette CNC sous Turbocad, je n’ai pas pu conduire les simulations qui vont bien ! alors je me suis fié au design des CNC pro …
Il faut faire attention aux capacités des patins, elles ne sont pas les mêmes en appui ou latéralement ; les patins des rails cylindriques supportés ont tendance à s’ouvrir légèrement (ça reste minime, mais …) sous l’effet des efforts latéraux, ce qui m’a conforté dans mes choix.
En tous les cas, la disposition “les 2 rails sur le coté, dans un même plan” me semble plus simple à construire (sinon, la réalisation de l’équerre en partie supérieure suppose un vissage sur champ, géométrie délicate à tenir), et surtout bien plus facile à régler (ce qui est une des grosses étapes de la construction d’une telle machine).
Michel
Bonsoir Michel,
J’hésitais entre ces deux possibilités, du coup vos arguments mon aidé a trancher .
dernière hésitation concernant la partie châssis avant de passer a l’étape commande, le rail prismatique me semble plus délicat a fixer directement sur le profilé ( 20mm au dessus d’une rainure de 8mm) sans compter qu’il va ce trouver décentré ce qui ce qui me semble pas forcement optimal pour la répartition de l’effort sur le profilé.
Du coup je pensais fixer en intercalant un plat qui reprendrait le principe de fixation des rails cylindrique, inconvénient, on alourdit la facture avec un peux de poids en supplément.
A votre avis cela vaut il le coup ?
Bien Cordialement
Jimmy
Jimmy,
réponse simple : si tu en as la possibilité (celle de réaliser des perçages précis), pas d’hésitation, interposes un plat d’acier étiré entre rail et profilé ; du 10, ça ne coûte presque rien, et le surcroit de poids ne peut être que bénéfique (à la limite, une tôle d’alu plutôt que de l’acier sur le portique, pour minimiser l’inertie ?).
Michel
Bonsoir Michel,
J’ai commandé toute la partie châssis et plaque alu 2017A pour le Portique hier soir.
J’ai retenu la solution du plat de 10mm pour placer les rails sur les profilés.
du coup Rail de 20mm, et vis a bille de 20.
J’en profite au passage pour vous poser quelques question ( pour changer).
Les vis a bille existe en version double NUTS (DFU 2005) est ce utile si l’on a besoin d’une précision de 5 centièmes ?
sur les 80*80 est il prévu de pouvoir tarauder en M8 les troues en bout de profiler ou éventuellement d’utiliser des vis M8 auto taraudeuse ?
Merci d’avance
Bien cordialement .
Jimmy
Bonjour Jimmy,
bon, bientôt encore une petite sœur … super !
La précision :
les moteurs pàp vont vraisemblablement faire 200 pas par tour, sur une vis au pas de 5 ça fait une résolution de 25/100 ; donc, au delà des divers jeux, ce qui va vraiment être important, c’est la linéarité de la vis-à-bille.
Coté écrou, lorsque je vérifie au comparateur, je ne mesure pas de jeu significatif (comparateur bas de gamme au 1/100), cela me semble en particulier dû au gros diamètre (20) de la vis.
Donc, sauf à choisir des vis de qualité avec une très bonne linéarité (aïlle le portefeuille), je ne pense pas qu’un double écrou s’impose.
Sur ma machine, dans l’alu je tiens toujours les 5/100 ; le sujet devient un peu délicat pour les alésages de roulement, en général c’est loctite si pas d’exigences sévères, ou reprise à la tête à aléser.
Pour les vis de 8 : je t’avoue tout ignorer du comportement mécanique d’une vis auto-taraudeuse, mais à priori je resterai sans hésiter sur des vis “classiques” (résistance, montage/démontage), les profilés Motedis se taraudent très bien (j’ai taraudé à la perceuse sans fil).
Michel
Bonjour Michel et merci pour ces infos,
Concernant la linéarité de la vis a bille , est ce que cela figure dans les tableaux des SFU2005 présent sur les différents site ?
Jimmy
La linéarité de la vis à bille dépend de sa classe de précision, rarement précisée sur les sites non pro ; regardes par exemple sur un site comme SKF, tu y trouveras pas mal d’explications.
Ce qui est certain, c’est qu’une vis de précision coutera extrêmement plus cher que celle que tu trouveras couramment sur les sites amateurs ! mais pour une précision de 5/100 (sur 10 à 20 cm de longueur), inutile heureusement d’aller jusque là …
Michel
Bonsoir Michel,
Quelques nouvelles du projet en cours,
J’ai reçus hier les profilés de chez MOTEDIS, visiblement il était en retard sur leur préparation de commandes (livraison sous 3 semaines).
ceci étant dit chez découpe Acier il non guerre été plus rapide.
L’essentiel c’est que du coté châssis et portique coté structure tout soit la, l’usinage va pouvoir commencer.
d’ailleurs au passage une fois n’est pas coutume, Une petite question : sur quoi a vous fait reposer le chassis profiler car je me demandait si malgré le bon niveau d’assemblage celui ci n’aurais pas tendance a ce déformer si l’on venais a le déplacer après assemblage et mise au point de la métrologie, ce qui aurais pour conséquence de devoir tout reprendre au niveau réglage.
qu’en a t’il été pour vous de ce point de vue ?
Bien Cordialement
Jimmy
Bonjour Jimmy,
Lors de l’assemblage et des réglages de géométrie, le plan de travail ne constitue en aucun cas une référence géométrique ; tout est affaire de règle, équerre, comparateur … j’ai choisi la table rainurée comme référence, cette dernière m’ayant été livrée avec un relevé de mesures très satisfaisant ; tout est calé par rapport à celle table, en la contraignant au minimum.
Il faut faire un stock de clinquants de diverses épaisseurs (1/100, 2/100, 5/100, 10/100) ; les réglages sont des opérations très fastidieuses car il faut pas mal itérer…
Par la suite, une fois la cnc terminée, je lui ai adjoint 4 pieds ajustables (motedis) et je l’ai posée sur une table assez peu rigide … donc lors des usinages ça bouge éventuellement ; mais, pour avoir vérifié plusieurs fois, ça ne bouge pas plus qu’admissible (1 à 2/100), moins que la précision de la machine.
En revanche, cette mauvaise liaison cnc/table n’est pas favorable à l’absorption des vibrations ; mais rien qui n’affaiblisse la qualité d’ensemble.
Michel
Ps : tu as reçu les profilés 80×160, une fois en main la confiance s’instore facilement !
Bonjour et bravo pour cette superbe réalisation !
Je ne vois pas comment est fixée la vis à bille des X, celle qui déplace le chariot sur les rails des X, pourriez vous m’aider à comprendre cette partie ?
jean
Bonjour Jean,
que ce soit pour l’axe des X (chez moi, perpendiculaire au portique) ou l’axe des Y, les vis de 20 sont “fixées” à leurs extrémités par 2 paliers (BK15 et BF15), coté moteur palier à 2 roulements obliques, à l’autre extrémité palier simple roulement droit ; ces paliers sont fixés sur des platines en alu de 10 (pour tenir compte des géométries respectives des paliers d’une part, des patins et du support de l’écrou de la vàb d’autre part), elles mêmes fixées sur le(s) profilé(s) alu, 80×160 latéraux pour les X et 80×80 supérieur pour les Y.
Michel
merci Michel pour ces précision
Bonjour Michel,
je découvre ce site en pleine construction de ma CNC pour… des panels d’A320! je me sens moins seul!D
pour revenir à la CNC, félicitation! elle semble parfaitement répondre à tes besoins, j’espère avoir cette “chance”! je met entre guillemets car j’ai pas mal travailler pour que ça marche!
je reviens sur ta gestion des câbles, et notamment sur les câbles blindés qui relient moteurs aux drivers
tu dis que les masses sont reliées au boitier en un point, mais où relies-tu le câble de masse côté moteur?
Merci!
Bonjour Vincent,
Voilà qui est sympa ! un nouvel A320 en vrai DIY (par opposition aux simus conçus à base d’éléments commerciaux …) ; si tu as besoin d’une quelconque aide, n’hésites pas à me solliciter.
Pour ce qui concerne le câblage de la CNC, non, pas de connexion aux moteurs, le blindage de chaque câble blindé n’est relié que d’un coté à la masse, point unique fixé sur le boitier ; en revanche, il y a un câble mono-conducteur qui relie directement la machine elle même à ce point de masse central ; la règle essentielle est : pas de boucle de masse ! Cela étant, tu noteras que le blindage des câbles moteurs ne sert pas à protéger les signaux qui y transitent (courants forts), mais bien plutôt à éviter que ces signaux ne perturbent les courants faibles avoisinants (par exemple les câbles des fins de course, qu’il convient d’éloigner le plus possible des câbles moteur).
Bonne continuation,
Michel
Merci pour ta réponse,
malheureusement je pêche un peu niveau électricité donc je ne suis pas sûr de bien comprendre et je ne voudrais pas faire de bêtise!
mes moteurs ont 4 fils, je vais prendre 1 câble blindé 4 fils + 1 masse, donc je vais relier tous les fils de masse venant de mes moteurs à un point sur le boitier (tu l’as relié à tes connecteur db9), et c’est tout?
y a t’il nécessité d’après toi de protéger les courants faible par un câble blindé pour justement limiter les interférences?
Merci!
Oui, c’est tout : le blindage de chaque câble moteur au point commun de masse sur le boitier, tu peux bien sur passer par les db9.
Et oui, il faut absolument blinder les signaux faibles.
Michel
super tu a de la chance apparament tu a de tres bonne connaissance en electronique et c’est la Mon probleme pour la mienne c’est dans cette parties que sa ne vas pas du tout je galere et j’en n’est marre
car sa traine depuis plusieurs mois et la suis a me demander si sa en vaut encore le coup serieusement ….
Bonjour Daniel,
Ne te décourages pas comme ça, nul besoin de connaissances en électronique pour la CNC, juste un peu de câblage assez basique ; il te faut juste un plan correct, mais là aussi, c’est vraiment simple, peut-être devrais-tu faire valider le tien, ici ou sur un forum.
Michel
Bonjour,
Je suis néo-retraité et j’envisage de réaliser une fraiseuse CNC. Bravo pour le résultat obtenu pour votre projet. Le cahier des charges correspond à ce que j’envisage. J’ai trouvé sur un autre site un fichier “Projet 6.tcw” qui correpond à votre fraiseuse. Il est réalisé sous TurboCad le crois, comment se procurer une version gratuite pour que je puisse voir un peu plus en détail car j’aurais beaucoup de questions … ?
Cordialement.
Régis
Bonjour Régis,
2 ou 3 longerons ? En fait, c’est une croix, donc 3 morceaux qui apparaissent comme 2 longerons qui se croisent !
Pour ce qui concerne Turbocad, il semble qu’il soit possible de se procurer une version d’évaluation chez Avanquest …
Cordialement, Michel
Bonjour Michel,
Je n’ai finalement pas pu charger TurboCad proprement. Je vais donc me lancer dans une conception en m’inspirant des choix que vous avez faits, et surtout je vais faire une évaluation grossière du coût avant de me lancer dans la réalisation. J’aurai certainement des questions à venir…
Cordialement.
Régis
Ah, désolé, c’est vrai que le monde Turbocad est super cadenassé … et hélas, les exports 3d dans d’autres formats que celui de Turbocad ne donnent rien !
N’hésites pas à poser des questions ; pour ce qui concerne les coûts, en achetant tout, au moment de la construction, ça tournait autour de 2000 €, mais les prix ont vraisemblablement évolué dans le bon sens.
Michel
Bonjour.
Très belle réalisation ! Bravo !
Réfléchissant en ce moment à une conception, la votre me rassure quand à la rigidité de l’ensemble (si souvent dénigré).
Vous noté que vos rail sont des profil série lourde, d’ou viennent-ils ?
Et votre table rainurée, qui a été votre fournisseur ?
Merci d’avance pour vos réponses.
Bon vol !
Bonjour Sébastien,
Les profilés alu viennent de chez Motedis, et en effet, plus ils sont lourds, mieux c’est !
Quand à la table rainurée, je l’ai achetée chez Ironwood, mais hélas, cette société a fermé … pas simple d’en trouver ailleurs, et en plus, c’est cher ; une table en acier irait tout aussi bien, voir même mieux, peut-être plus facile à trouver. A noter : je n’avais pas trouvé une table suffisament large, il manquait 40 mm en largeur ; j’ai compensé en rajoutant deux tubes alu 20×20 sur les cotés, là où de toutes les façons la broche n’ira jamais.
Michel
Merci pour vos réponse.
Je me doutais que c’était Motedis, mais d’après leur catalogue en ligne, ils ne font plus que la série légère …
Je vais chercher pour la table.
Le design que je suis en train de faire ressemble au votre, mais les traverses en 40×80 passent sous les poutres de 80×160, et le portique sera plus “ramassé” (80×160 aussi).
Comme ça je gagne en hauteur utile en améliorant la rigidité du portique.
Bonne continuation à vous.
Bonjour,
Magnifique réalisation, vraiment.
J’ai l’intention de réaliser une machine semblable pour travailler l’alu mais également modifier des meubles en chêne.
La question qui me taraude concerne la broche. Faut-il une broche refroidi à l’eau ou pas, car il semble que ce soit plus complexe et plus bruyant. Enfin, la puissance de la Kress 1050 fme-1 n’est-elle pas un peu faible comparer à une broche de 2.2 kW souvent conseiller pour le travail de l’alu, surtout en tenant compte de cette très belle construction ?
Merci de vos conseil avisés.
Bonjour Jean, et merçi pour le compliment !
Je pense que les broches des machines d’amateur sont souvent trop puissantes, le calcul des efforts de coupe dans l’alu avec de petites fraises (max diam 10) le montre bien.
A partir de là, une broche de 2,2kw, c’est nettement trop, et en plus c’est très lourd (le moteur du Z va chauffer sérieusement !) ; coté nuisance sonore, le refroidissement par eau est plus silencieux que par air ; de ce point de vue, la kress est assez bruyante, mais quand on est dans l’alu, pas sur que ce soit la broche qui fasse le plus de bruit !
Le vrai sujet me semble ailleurs :
– vitesse plancher (avec encore du couple), les broches chinoises (celles que tu évoques et que l’on voit partout, 1,5 kW ou 2,2 kW) tournent bien vite dans l’alu, ou plutôt ne descendent pas suffisament bas en régime ; donc conditions de coupe dégradées, usure rapide des fraises …
– équilibrage et concentricité : là, il faut bien faire attention aux roulements qui équipent la broche.
J’utilise la kress depuis près de 10 ans, elles viennent (venaient) avec un certificat de concentricité, et j’en suis globalement satisfait ; un reproche, le profil de la coque, qui rend un peu délicat le dessin d’une double bride de fixation (au regard de sa conception, la seule fixation par le colet est un peu légère dans l’alu).
En fait, il n’y a pas tellement de choix, pour avoir mieux, il faut mettre beaucoup plus d’argent !
Michel
Merci Michel,
C’est un vrai plaisir de te lire, car tes réflexions sont de bons sens et me rassure quant à la suite de mon projet, car comme toi je préfère mettre de l’argent dans les profils qui sont la base plutôt que dans le moteur qui peut toujours être changer en cas de soucis, mais visiblement ce n’est pas le cas. Je suis d’accord avec toi les broches tournent beaucoup trop vite.
Ancien fraiseur dans ma jeunesse, j’étais plus habitué à faire tourner les fraises à 1000 ou 2000 tours, là on part en survitesse avec ces moteurs.
bon Week end.
Jean
bonjour,
votre réalisation est très intéressante, je pense m’en inspirer largement pour un projet que je démarre. de toutes les réalisations que j’ai rencontrées sur Internet, elle est (pratiquement) la seule à utiliser le guidage de l’axe X en fixant le rail en dessous du portique et pas latéralement. pour des rails prismatiques, il me semble que ce choix est le meilleur. il présente toutefois une difficulté: obtenir la perpendicularité du rail avec le montant latéral du portique. pourriez-vous détailler votre montage de cette partie et les réglages.
cordialement.
Olivier
Bonjour Olivier,
merçi pour ce commentaire, cette réalisation a en effet sucité de nombreuses répliques …
Je ne comprends pas en revanche votre question : le guidage de l’axe des X (qui va de l’arrière à l’avant) est assuré par 2 guides supportés placés sur les profilés latéraux, celui de l’axe des Y (transversal, sur le portique) est assuré par 2 guides supportés fixés latéralement, sur les faces verticales des profilés du portique.
Les réglages d’orthogonalité sont en effet importants, nombreux et assez fastidieux, je peux détailler ; je n’ai eu à utiliser du clinquant que pour la fixation de la table rainurée sur les profilés de la base, pour le reste le jeux entre trous de fixation et vis (environ 5/10) est largement suffisant, je n’ai pas goupillé mais à l’usage il s’avère que ça n’a pas bougé.
Michel
bonjour,
pas facile de poser des questions compréhensibles par le lecteur…
mon interrogation portait sur l’axe X : comment obtenir l’orthogonalité de la platine horizontale qui coulisse sur le rail de l’axe X et de la plaque verticale qui la surmonte. les équerres visibles sur les photos me laissaient perplexe. votre réponse est claire : il est possible d’ajuster la position des pièces jusqu’à obtenir l’orthogonalité.
enfin, pourriez-vous préciser si vous aviez vissé ensemble les deux plaques, autrement qu’avec les équerres?
bien cordialement.
Olivier
Bonjour Olivier,
L’équerrage des 2 platines horizontales du portique est presque un non sujet :
1) bien sur, les champs des flans du portique doivent être bien d’équerre (ponceuse lapidaire),
2) puis assemblage du portique, les 2 poutres horizontales, les 2 flans, et les 2×3 équerres de fixation sur les platines,
3) il suffit ensuite de poser le portique sur un plan, de bien faire reposer les 2×3 équerres sur le plan, et de fixer solidement ces équerres.
4) les 2 platines seront automatiquement bien positionnées dans le plan horizontal, mais de toutes les façons ça n’est pas absolument essentiel.
Dans cette affaire, l’important est la bonne géométrie du portique : les 2 poutres exactement de même longueur et parfaitement coupées, et les 2 flans bien identiques (contre-perçage des trous de fixation des poutres horizontales).
La fixation du portique sur les platines repose exclusivement sur les 6 équerres, et sert à régler l’orthogonalité X/Y une fois les 2 vàb X en place (cette fixation peut d’ailleurs faire office de fusible en cas de perte de pas sur l’une des 2 vàb X)
Rassures-toi, cette fixation est parfaitement fiable, je n’ai jamais eu l’ombre d’un déréglage.
Michel
bonjour Michel,
un grand merci pour le temps que tu passes à répondre à mes questions de néophyte.
bien cordialement.
Olivier